EptaService is getting ready for tomorrow today.
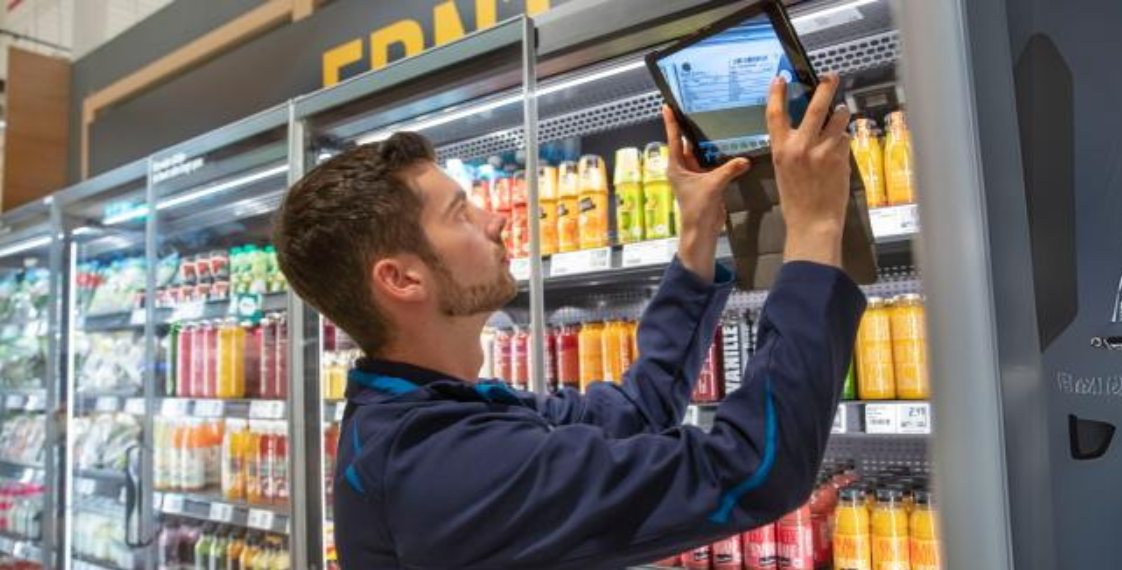
They are on the road every day, ensuring that refrigeration units and cooling systems operate smoothly: the employees of EptaService. Service Manager Klaus Corban explains how the department is addressing new challenges and preparing for the future.
It has evolved into one of the largest service organizations in commercial refrigeration technology in Germany: the EptaService department. According to Service Manager Klaus Corban, the reasons for this are diverse. However, the foundation lies in the highly trained employees who offer a full range of services – from cleaning refrigeration units to repairs and maintenance, to retrofitting refrigeration systems. Behind this are the employees in the service center, who are available around the clock. Customers benefit from having a personal contact person there. 'Our service organization is very efficiently structured and operates extremely reliably,' says Klaus Corban. 'Nevertheless, we want to continue training and further educating our technicians.
For this purpose, we are currently planning our own training center in Mannheim. This way, we can ensure that all employees are optimally qualified in the future, as the equipment technology is becoming increasingly complex and our work is becoming more digitally integrated.
The number of apprentices is increasing
With the new training center, the company aims to prepare for future market challenges. The shortage of skilled workers also affects the refrigeration industry. Despite the service department already comprising around 300 employees, Epta could hire even more. 'To counteract the shortage of skilled workers and ensure an adequate workforce in the future, we are continuously increasing our apprenticeship quota,' explains Klaus Corban. 'From the current 25 apprentices per year, we aim to reach 75.' It's an ambitious goal, which requires a lot of communication and participation in numerous job fairs, confirms the service manager. 'The apprenticeship as a mechatronics technician specializing in refrigeration technology is still not widely known, so we introduce Epta and the apprenticeship program at job fairs – even at the Berlin Olympic Stadium. However, the best advertisement is still a good, attractive, and future-proof apprenticeship; word of mouth is essential.' Also included are annual events or a trip to Italy to visit the production facilities of the Epta Group.
Stronger Together
The global delivery difficulties are likely to soon affect Epta as well. While the company has large stocks of spare parts in storage, these are also finite. 'We will need to learn to cope with long delivery times. However, so far, we can still deliver spare parts as requested,' describes the service manager the current situation and continues, "Our order volume is enormous at the moment. We can only manage this because we have such a great team, and I can rely on all my colleagues 100 percent. Nevertheless, we are always working to improve processes and procedures - which ultimately also benefits our customers."
To maintain our systems proactively
Challenges and opportunities alike, digitalization presents itself to Epta Service. In this regard, the department aims to equip customers' refrigeration systems with monitoring systems that transmit information about temperature, fill levels, and similar parameters to a central location. This approach could enable predictive maintenance in the future. For grocery retailers, this would mean increased security and reduced downtime. Epta could optimize workforce scheduling because employees would no longer need to be dispatched on demand to address issues for customers.
Electrify the fleet
With the end of the combustion engine in the coming years, EptaService faces another challenge: The service department's fleet comprises around 240 vehicles that need to be gradually converted to electric vehicles. "So far, there hasn't been a real alternative for us," explains Klaus Corban. "We will soon receive an electric motor VW van for testing. I hope that we can clarify some questions then." Because there are quite a few open questions: What does the charging infrastructure look like until then? Is the range of the vehicles sufficient? What payloads are possible?